Klima- und Umweltschutz beginnt im Unternehmen.
Vorreiter sein – diesen Anspruch verfolgen wir nicht nur mit unseren Produkten, sondern auch mit umweltschonenden, energie- und ressourceneffizienten Produktionsprozessen. Eine weltweit einheitliche, ambitionierte Umwelt- und Energiepolitik schafft dafür die Grundlage.
Teilprojekte der „Sustainable Factory“, als Bestandteil der Initiative „Factory for Tomorrow“, wurden im Rahmen des Zukunftsprogramms „Agenda 4 plus One“ gestartet.
Wo wir stehen
Wir haben die Projektverantwortlichen nach ihrer subjektiven Einschätzung gefragt:
Wie weit ist die Pilotierung der CO2-neutralen Fabrik?
Wie viel vom Potenzial der 3D-Drucktechnologie hat Schaeffler bereits ausgeschöpft?
Abdeckung Produktionsstandorte mit Energiemanagementzertifizierung ISO 500011)
Mit unternehmensweit gültigen Energie- und Umweltmanagementsystemen steuern wir unsere Aktivitäten. Ihre Umsetzung wird von unabhängigen Experten geprüft.
1) Bezogen auf Mitarbeiter
Unser Ziel: die nachhaltige Fabrik
Wir arbeiten stetig daran, unsere Produktionsprozesse zu verbessern: etwa durch ein systematisches Energiemanagement, den Einsatz ressourcen- und materialsparender Technologien oder die Vermeidung beziehungsweise Wiederverwertung von Produktionsabfällen. Mit dem Konzept der „Sustainable Factory“ verfolgen wir dabei einen ganzheitlichen Ansatz. So werden beispielsweise Fertigungs- und Logistikprozesse digitalisiert, damit Maschinen und Prozesse zentral gesteuert und im Hinblick auf ihre Effizienz optimiert werden können. Der Ansatz beinhaltet auch Nachhaltigkeitsstandards für die Beschaffung von Produktionsmaschinen und die Errichtung neuer Gebäude.
Nicht zuletzt werden auch die Bedürfnisse unserer Beschäftigten berücksichtigt. Architektur und Ausstattung der „Factory for Tomorrow“ unterstützen flexible Arbeitsabläufe und fördern den persönlichen Austausch. Mehr zu diesen Themen finden Sie unter „Umwelt und Energie“.
Anlieferung, Zwischenlagerung und Distribution unter einem Dach – der zentrale Wareneingang in Herzogenaurach ist ideal als Pilotprojekt für nachhaltige Energieerzeugung, -speicherung und -nutzung. Alle Prozesse sollen künftig rund um die Uhr mit Solarenergie laufen.
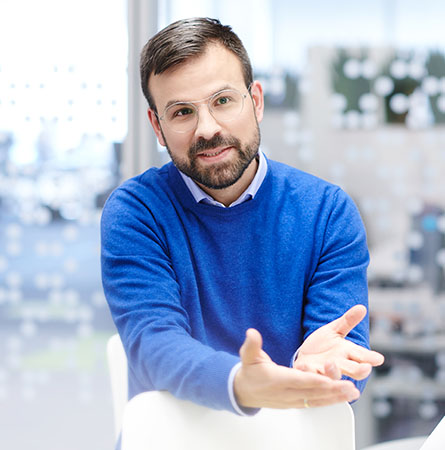
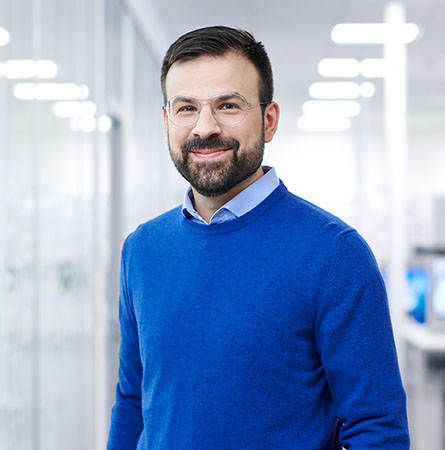
„Unsere Produktinnovationen sind nicht nur für unsere Kunden ein Gewinn. Dank unserer neuen Stromspeicher wollen wir die ‚Sustainable Factory’ stabil mit grünem Strom versorgen.“ Christian Adler, Corporate Factory Planning, Leiter Workstream Sustainable Factory
Auf das Dach des Wareneingangs kommt eine Solaranlage. Sie wird den Energiebedarf des Gebäudes decken sowie Strom für Ladestationen und zur Erzeugung von Wasserstoff für Brennstoffzellen liefern. „Damit der Strom auch fließt, wenn die Sonne nicht scheint, setzen wir auf eine skalierbare Speicher technologie aus einem Joint-Venture“, erklärt Adler. Diese basiert auf nachwachsenden Rohstoffen und steht kurz vor der Marktreife.
Hochwertige Bauteile aus dem Laserdrucker? Additive Fertigung – auch 3D-Druck genannt – heißen Verfahren, bei denen Werkstücke nicht mehr aus einem festen Block herausgearbeitet, sondern Schicht für Schicht unter anderem aus einem pulverförmigen Ausgangsstoff aufgebaut werden.
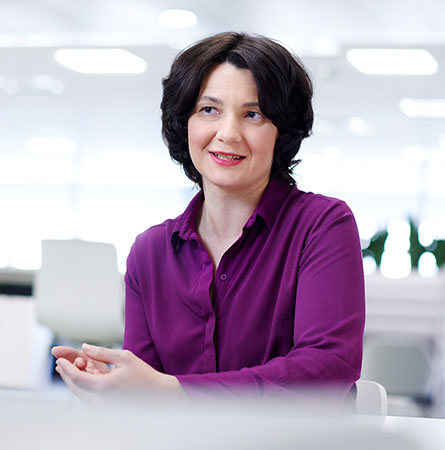
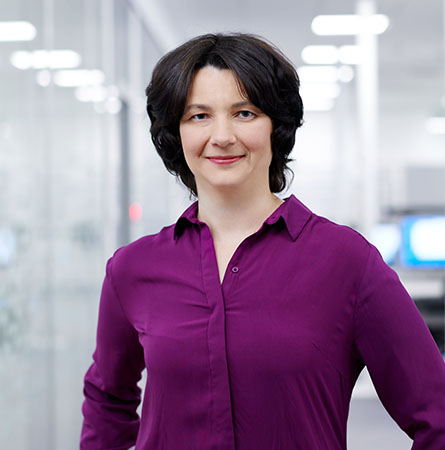
„Das Potenzial der Additiven Fertigung ist noch lange nicht ausgeschöpft. Richtig eingesetzt, können wir deutliche Einsparungen bei Material, Kosten und Fertigungszeit erzielen.“ Ruslana Mys, Spezialist Entwicklung Produktionstechnologie
Jährlich produziert Schaeffler in Herzogenaurach etwa 5.000 Teile per Additiver Fertigung – mit steigender Tendenz. „Nicht nur Anschauungsmuster werden auf diese Weise hergestellt, sondern auch hochwertige Prototypen und Werkzeuge für den Serieneinsatz“, berichtet Mys. 2015 haben wir einen eigenen Bereich für Additive Fertigung gegründet und erschließen immer neue Einsatzmöglichkeiten.
Additive Verfahren im Vorteil
Der sogenannte „Doppelkammkäfig“ ist ein zylindrischer Hohlkörper, der in Wälzlagern zum Einsatz kommt. Mithilfe additiver Verfahren lassen sich hierbei 14,5 kg Material für den Rohling sparen.